Why choose ACE remanufactured transmissions?
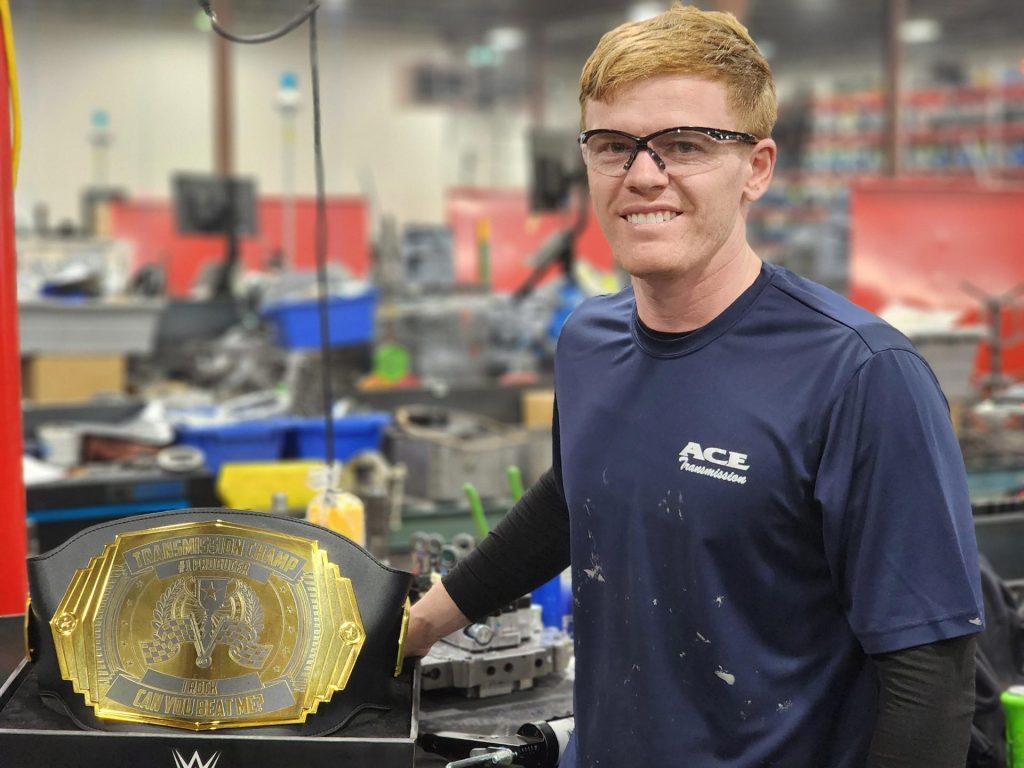
Table of Contents
Increase profits at your automotive repair shop
The more money your business generates, the greater the financial impact you can have on your family and your employees. We are passionate about creating products and systems that help you increase sales volume, decrease costs, and build an extremely valuable business.
We help increase your profits in these important ways:
How the quality of ACE remanufactured transmissions can boost your profits
Buying high-quality parts is critical when operating a highly profitable automotive repair shop. Consider these two scenarios:
Poor-quality versus high-quality remanufactured transmissions
Poor Quality
Poor-quality units are more likely to fail, which leads to unhappy customers who bad-mouth you all over social media. Unit failures also cause …
High Quality
High-quality units are more likely to perform well. Happy customers become powerful word-of-mouth advertising advocates for your business. You’re not busy redoing your work, so …
That’s why we’re dedicated to providing the highest possible quality remanufactured transmissions, quickly, and at a profitable rate. We invest a lot of time and money into the important factors that drive quality: R&D, testing, and training.

Great research-and-development strategies discover the best techniques and part selections
Historical data tracking
We keep meticulous records to discover which parts work well and which parts don’t. This helps us build the best transmissions in the industry—possibly even better than the original manufacturer’s units!
We track the entire lifecycle of each and every part of our factory:
- Where we purchased each part and core
- The core vehicle’s VIN
- Who built each of our remanufactured units
- Each part that goes into each remanufactured unit
- Which dyno testing machine it ran on
- Which dyno operator tested it
- The results of the dyno tests
When we have a warranty claim, we investigate the unit thoroughly to determine what went wrong and how to prevent that type of failure in the future. It may have been a problem with a parts dealer. In that case, we could consider switching to another vendor.
Units designed specifically to fit that exact vehicle
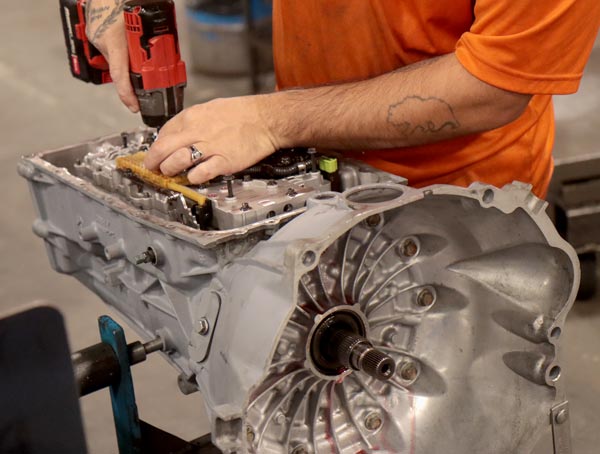
We build each unit part to fit a specific application – based on a specific vehicle year, make, model, and engine. We say, “If it’s not the right one, it’s the wrong one.” Our units must be built to the OEM specs.
Some other remanufacturers are much less specific when building units. They will try to sell cookie-cutter products in bundles of “similar” units, which they consider to be “close enough” to the OEM specs. We don’t do that.
Even though another “similar” unit will technically fit on a vehicle and function, it probably won’t perform 100% correctly all the time and probably won’t last as long. Accumulators and springs in each unit should be specifically designed for a particular vehicle.
It’s like if you fit in a medium-sized shirt, you can fit in a large as well, but it’s not ideal. But when you order a transmission from ACE, you can be sure it will fit and perform as well as the original unit (or better).
High-tech quality testing helps prevent failures before they happen
We have some of the best builders in the industry. But we still verify their great work with high-tech testing procedures and detailed analysis. It’s our goal to minimize unit failures so you can maximize profits.
- Quality testing: All units are tested on high-tech, custom-built dyno machines that simulate a wide variety of real-world driving conditions on each unit before it’s shipped. If there is any concern with a unit, it goes back to the builder for correction.
- In-depth quality inspections: Our research-and-development team performs random quality control inspections, taking units completely apart and looking for any possible concerns. The same goes for a dyno failure or a warranty failure. This holds the builders personally responsible for the quality of their work.
We’ve been training transmission experts for 40+ years
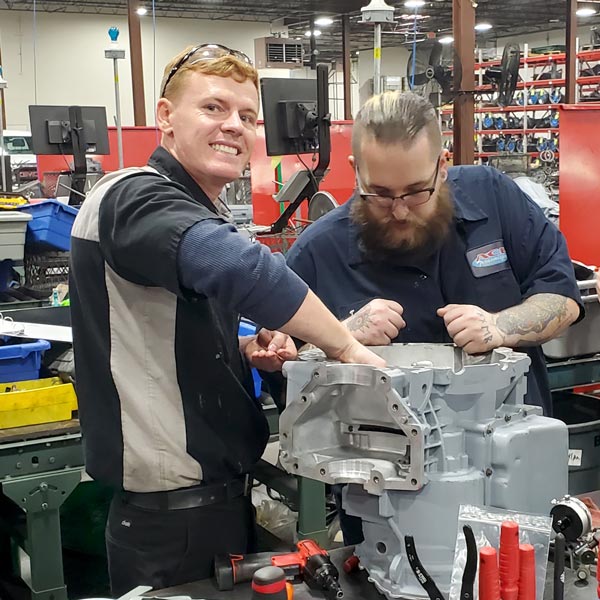
We are constantly training our team of expert transmission builders. We ensure they never stop learning, so we can keep up with this ever-changing industry and deliver great results for decades to come. We invest in our employees to deliver better results for our wholesale clients.
- In-house training program: We developed an extensive 12-week training program, overseen by our highly experienced industry veterans. Plus, new employees are supervised and tested by more experienced team members.
- ASE-A2 certified: Our transmission builders are required to earn their Automatic Transmission certification from the National Institute for Automotive Service Excellence, which proves their expertise through a third-party industry authority.
- ATRA certified: They must also earn the Automatic Transmission Rebuilders Association certification.
- Continuing education: Every builder is required to spend two hours per week in our in-house classroom, learning the latest training – forever.
- Quality incentive program: Our team members are held to the highest standard and are financially motivated to perform with excellence. They are rewarded for great work and held responsible for errors.
How our amazing warranty promotes & protects your profits
When your auto shop offers a valuable warranty to your potential customers, you can get more sales, faster, with a higher asking price. That’s why ACE Transmission Remanufacturing includes an amazing warranty on every unit we sell.
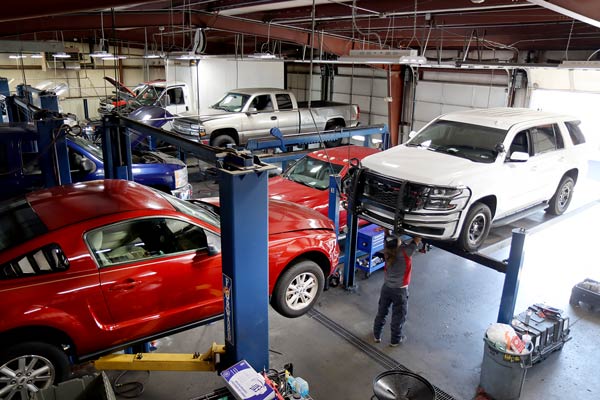
What’s included
When you sell ACE units, your customers get all of these benefits:
- 3-year, unlimited mileage, warranty
- All transmission parts
- The labor to install them
- Mobil 1 transmission fluid reinstalled
- Coast-to-coast nationwide coverage
- Transferable to the next owner
Learn more
Coast-to-coast coverage
Our 3-year, unlimited mileage, warranty doesn’t just work at your local repair shop – it’s a nationwide warranty. If you put a transmission in a customer’s vehicle, then they drive across the country and it fails, we will still take care of it at the nearest repair facility. We want your customers back on the road as quickly as possible, so they are happy. Happy customers tell their friends 🙂
How our fast process helps your business grow faster
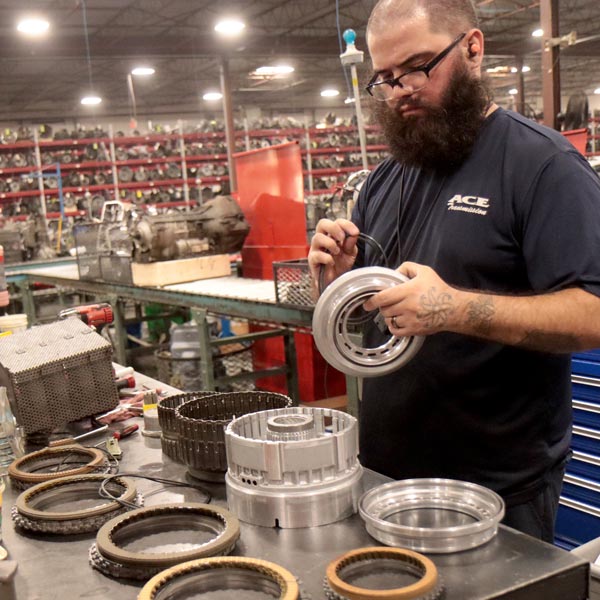
Back in the old days, most auto repair shops rebuilt automatic transmissions in-house. But, these days transmissions have changed and become much more complex. Rebuilding units takes lots of time, specialized tools, and ever-changing employee training.
That’s why ACE Transmission Remanufacturing builds units on your behalf, using highly trained experts and specialized equipment in our high-tech facility.
Once you become a wholesale buyer, your shop can be more profitable and service a higher volume of vehicles – faster, with better bay efficiency.
Learn more about why remanufactured transmissions are a better choice than rebuilt units.
Shipping options
We use our trucks to deliver to the local Springfield, Missouri, area. For clients outside of the metro area, we use LTL freight carriers.
To simplify things, we can arrange the freight on your behalf. When buying a single unit, the client pays the cost of shipping, both ways. We’ll do all the logistics work and bill you later. For our higher-volume wholesale distributors, the cost to return the units may be covered by ACE.
We can get a unit to any corner of the United States in three or four days.
???? Each remanufactured transmission unit comes with:
- Transmission fluid
- Torque converter
- Special brackets to hold the unit in the tote, as needed
- Detailed installation instructions for that exact unit and vehicle
Our Premium Eco-Friendly Shipping Totes
We try to use the best parts to give you the best quality – even when it comes to things like shipping totes. Most of our units ship in premium containers designed specifically for transmission delivery. These are the best totes available. They protect your unit from being damaged in transport, so it’s ready to install at your shop.
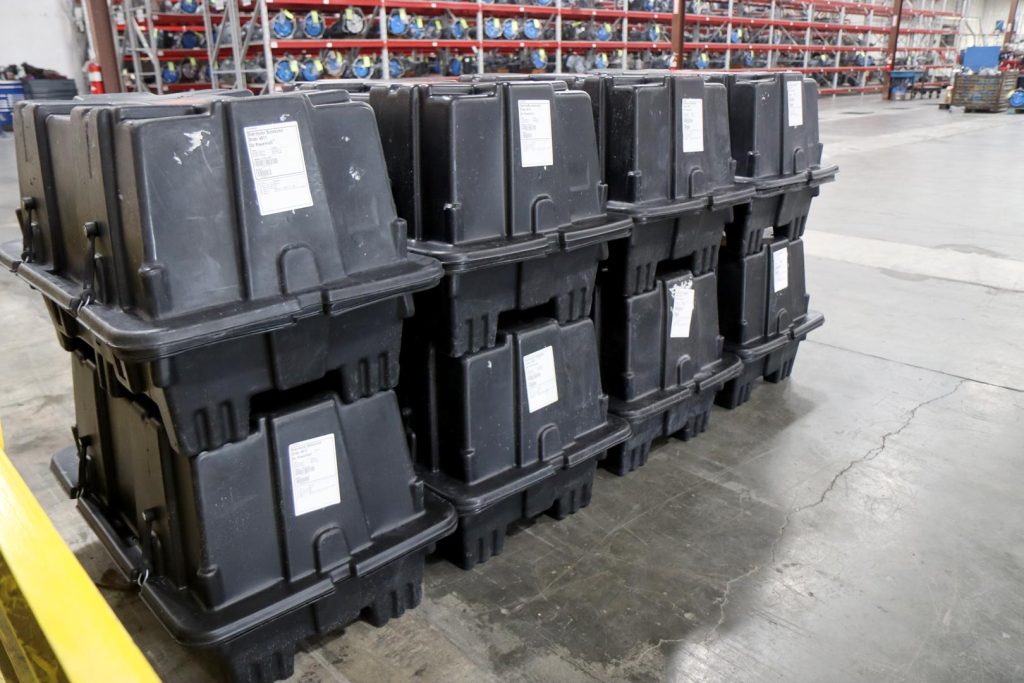
How to return your transmission core
Once you have the remanufactured unit installed, place the old core into the same shipping tote and call us to arrange shipping back to our factory.
Once the core arrives at our facility, our inventory team inspects it for quality and correctness (It’s possible the vehicle had previously received an inferior “cookie cutter” unit from another remanufactured). If there are no problems with the core, we mark the client’s account as not being financially responsible for the core cost.
We wash the tote and use it again. Using the same totes over and over again is a more environmentally friendly option than using wooden crates that are thrown away after each use.
We understand shop owners because we are shop owners
We’ve been running a retail transmission repair shop for over 40 years.
Marvin Gott launched ACE Transmission in 1981, with the support of his wife Darla. ACE Transmission grew from a tiny, one-man shack to become the undisputed #1 transmission repair and remanufacturing company in Southwest Missouri.
We now have a total of 21 vehicle bays indoors – plus a huge lift outside that can handle large work trucks, buses, and RVs. We typically have 60 to 80 vehicles on the property!
We’ve been here for more than 40 years and have a second generation working within this family business. So ACE Transmission will be standing behind our work for years to come.
We want to share this success with you by sharing decades of valuable industry knowledge. Because our success depends on your success.